Introduction
Square galvanized steel tubes are one of the most widely used materials in modern construction, infrastructure, and industrial manufacturing. Their popularity is driven by their excellent corrosion resistance, structural strength, cost-effectiveness, and versatility. A crucial specification for square steel tubes is wall thickness, which directly affects the tube’s strength, weight, load-bearing capacity, and end-use applications.
This article explores the common thickness specifications for square galvanized steel tubes, their manufacturing standards, applications, benefits, and selection tips. Whether you are a wholesaler, contractor, or project manager sourcing steel materials, understanding the appropriate thickness is critical for ensuring safety, compliance, and optimal performance.
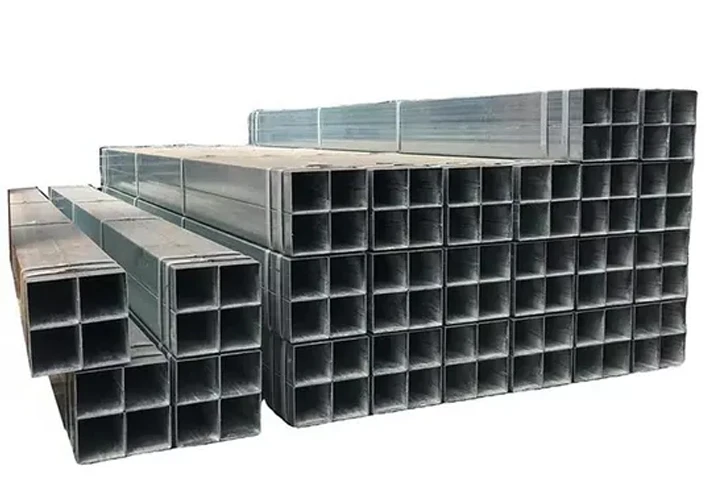
What Is a Square Galvanized Steel Tube?
A square galvanized steel tube is a hollow structural section (HSS) made from low-carbon steel and shaped into a square cross-section. The tube is then coated with a layer of zinc through either hot-dip galvanizing or electro-galvanizing, providing protection against rust and corrosion.
Key Characteristics:
- Shape: Square
- Material: Mild carbon steel (Q195, Q235, Q345, etc.)
- Coating: Zinc (galvanized)
- Surface finish: Shiny silver or matte (depending on galvanizing method)
- Standards: ASTM A500, EN 10219, JIS G3466, GB/T 6728
Why Thickness Matters
Wall thickness determines:
- Structural strength: Thicker walls offer higher load-bearing capacity.
- Corrosion resistance: Thicker steel may retain protective layers longer under harsh environments.
- Weight: Heavier with increased thickness; affects shipping and installation.
- Cost: Thicker materials require more raw steel, increasing cost per meter.
Common Thicknesses of Square Galvanized Steel Tube
Thickness is usually expressed in millimeters (mm) or gauge (in some regions). Here are the most common thicknesses:
Thickness (mm) | Gauge (approx.) | Application Examples |
---|---|---|
0.8 mm | 22 | Light framing, display racks, fencing |
1.0 mm | 20 | Furniture, light construction frames |
1.2 mm | 18–19 | Greenhouses, gates, temporary structures |
1.5 mm | 16–17 | Window frames, handrails |
2.0 mm | 14–15 | Support beams, guardrails, machinery frames |
2.5 mm | 13 | Light industrial frames, scaffoldings |
3.0 mm | 11–12 | Warehouse racks, solar panel supports |
4.0 mm | 9–10 | Structural construction, bridges |
5.0 mm | 8 | Heavy-duty industrial structures, support columns |
6.0 mm and above | 7 or thicker | Specialized heavy load-bearing infrastructure |
Factors Affecting Thickness Selection
When selecting the appropriate thickness for a square galvanized steel tube, consider the following:
4.1 Load Requirements
- Higher loads require thicker tubes to avoid bending, cracking, or collapsing.
- For structural applications, use ≥2.5 mm thickness.
4.2 Environmental Conditions
- In marine or humid environments, thicker steel resists corrosion longer, especially with hot-dip galvanized coatings.
4.3 Welding & Fabrication
- Thicker walls are easier to weld for strong joints.
- Thinner tubes are more suitable for bending and cold forming.
4.4 Cost vs. Performance
- Thicker tubes cost more due to increased steel usage.
- Choose thickness that balances strength and budget.
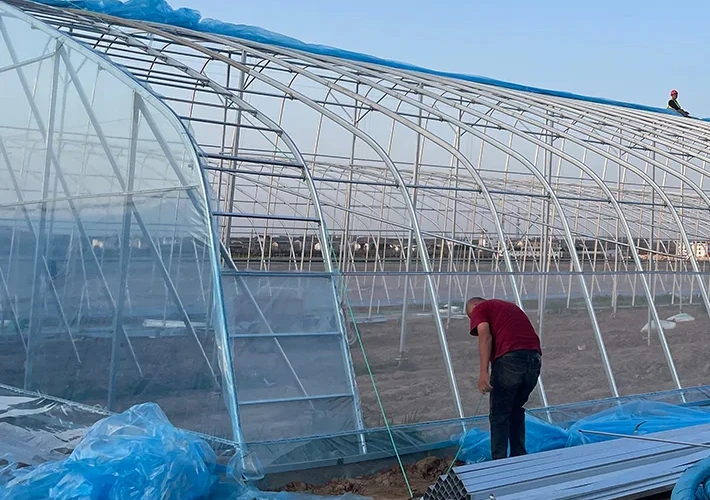
International Standards & Thickness Tolerance
5.1 ASTM A500 (U.S. Standard)
- Thickness tolerance: ±10%
- Thickness commonly from 1.5 mm to 6.4 mm
5.2 EN 10219 (EU Standard)
- Tolerance: ±10%
- Wall thickness: 1.0 mm – 12.5 mm
5.3 GB/T 6728 (China Standard)
- Common thickness range: 0.8 mm to 6.0 mm
- Tolerance depends on production method
5.4 JIS G3466 (Japan Standard)
- Used widely in Southeast Asia
- Popular thicknesses: 1.2 mm to 4.0 mm
Applications of Different Thicknesses
6.1 Thin Wall Tubes (0.8 – 1.5 mm)
- Light-duty applications
- Examples: furniture frames, curtain rods, decorative structures
- Advantages: lightweight, easy to handle, cost-effective
6.2 Medium Thickness (2.0 – 3.0 mm)
- Moderate strength and durability
- Examples: solar panel mounting, school furniture, fencing, gates
- Advantages: good balance of weight and strength
6.3 Thick Wall Tubes (4.0 – 6.0 mm and above)
- Heavy-duty structural applications
- Examples: building columns, warehouse racking systems, load-bearing frames
- Advantages: superior strength, longer lifespan, greater resistance
Manufacturing Process Overview
Raw Material Selection: Steel coils or plates of required grade
Forming: Cold forming into square cross-section
Welding: High-frequency welded seam
Galvanizing:
- Hot-dip Galvanizing: Full immersion in molten zinc
- Electro-galvanizing: Zinc applied using electrochemical methods
Sizing and Straightening
Cutting to Length
Quality Control: Thickness testing, zinc layer testing, dimensional accuracy
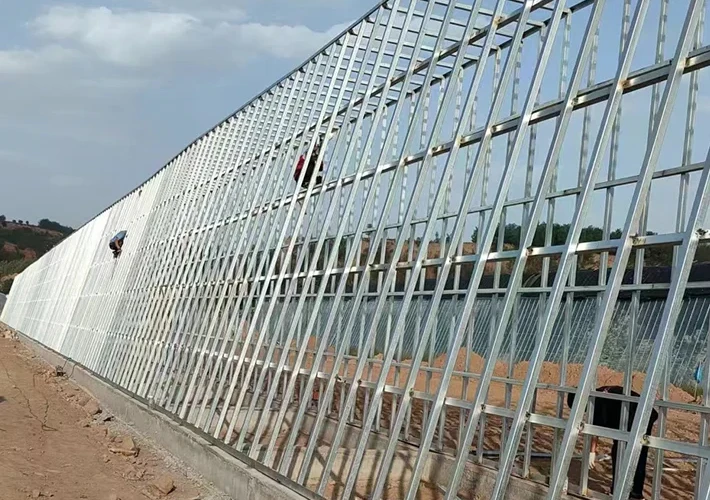
Thickness Testing Methods
- Ultrasonic Thickness Gauge: Non-destructive testing
- Micrometer/Caliper Measurement: Manual checking
- Coating Thickness Meter: Measures zinc layer and total wall thickness
Customization & Special Orders
Some manufacturers offer custom thickness options beyond standard ranges:
- Special projects: Bridges, offshore platforms
- Architectural design: Specific visual or strength requirements
- OEM/ODM service: Custom size, thickness, zinc coating layer
Tips for Buyers and Importers
- Clarify wall thickness tolerance: Especially for high-precision applications.
- Specify galvanizing method: Hot-dip offers better long-term protection.
- Request MTC (Mill Test Certificate): Confirms compliance and thickness.
- Sample inspection: Ensure supplier meets thickness specification.
- Ask for actual vs. nominal thickness: Nominal 2.0 mm may be 1.9 mm in practice.
Case Study: Thickness Selection in Practice
A construction firm in South Africa was building a commercial greenhouse. After evaluating the structural load, environmental conditions, and cost, they selected:
- 40×40 mm square tube
- Wall thickness: 1.5 mm
- Hot-dip galvanized (zinc coating ≥ 275 g/m²)
The material balanced structural strength and anti-corrosion for a 15-year lifespan. Later, for warehouse expansion, they used 3.0 mm thick tubes for the storage racks.
Market Trends and Demand for Various Thicknesses
- Southeast Asia & Africa: High demand for 1.5 – 2.5 mm thickness for infrastructure projects.
- Europe: Preference for precise EN standards, with higher tolerance requirements.
- Middle East: Popular sizes include 2.0 mm and 3.0 mm for hot environments.
- Latin America: Cost-effective thin-wall tubes for temporary structures.
Conclusion
Wall thickness is one of the most critical specifications when selecting square galvanized steel tubes. From light-duty applications with 1.0 mm thick tubes to heavy structural uses requiring 6.0 mm or more, each thickness serves a distinct purpose.
Understanding the common thickness options, their applications, international standards, and market preferences allows engineers, importers, and distributors to make informed decisions. As the global construction and manufacturing industries continue to grow, the demand for high-quality, properly specified square galvanized tubes remains strong.
For B2B buyers, partnering with a reliable steel tube manufacturer that offers full customization, strict quality control, and documentation is key to securing long-term success in the global marketplace.