Picture this: a sprawling industrial warehouse under construction. Overhead, crews are swiftly securing long, distinctive corrugated metal sheets onto the purlins. These aren’t just any sheets – they are IBR profile sheets, chosen specifically for their strength, efficiency, and the precise common size selected to meet the structural and budgetary demands of this major project. This scene plays out globally, where selecting the right IBR sheet common size is a fundamental, make-or-break decision for architects, engineers, and procurement managers. Get this choice right, and the project flows smoothly; get it wrong, and it leads to costly delays, compromised structural integrity, and budget overruns.
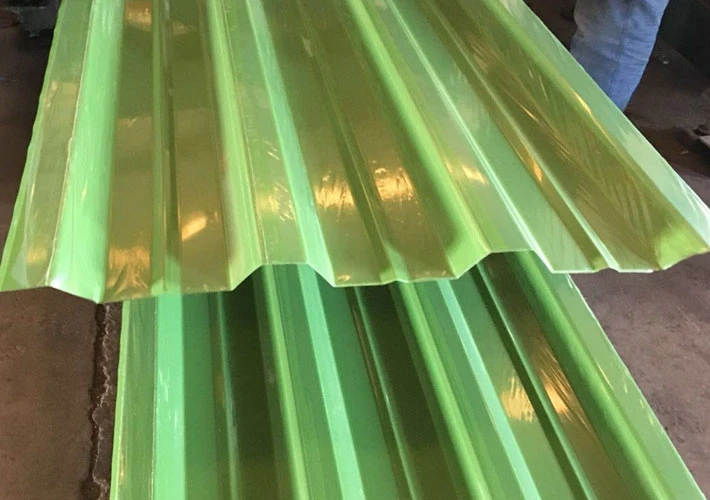
Understanding IBR Sheets: The Backbone of Modern Construction
IBR, standing for Inverted Box Rib, represents a pinnacle in modern profiled steel sheeting design. Its unique profile features a broad, flat pan section interrupted by symmetrical, trapezoidal ribs tapering to a narrow valley, then rising sharply to form the next rib. This isn’t just an aesthetic choice – it’s engineering brilliance.
- Structural Superiority: The deep, closely spaced ribs act like miniature I-beams running the sheet’s length. This dramatically increases spanning capability and load-bearing capacity (both live loads like maintenance personnel and dead loads like snow) compared to simpler corrugated profiles. IBR sheets can often span greater distances between structural supports (purlins), potentially reducing the overall steel frame cost.
- Exceptional Water Shedding: The pronounced ribs and sharp angles create definitive channels. This design ensures rapid and efficient water runoff, significantly minimizing the risk of capillary action or water pooling that can lead to leaks – a critical factor for roof integrity.
- Enhanced Stiffness & Durability: The complex profile geometry inherently provides greater resistance to bending (both along and across the span) and improved resistance to foot traffic during installation and maintenance without permanent deformation. This translates directly to long-term performance and reduced denting.
- Optimal Material Efficiency: Despite its strength, the IBR profile achieves excellent strength-to-weight ratios. This means less raw material is needed per square meter of coverage compared to some alternatives, contributing to cost-effectiveness and potentially lighter overall roof structures.
Decoding “Common Size”: Why Precision Matters in IBR Procurement
In the context of IBR sheets, “common size” refers to the widely available, standardized combinations of thickness (gauge), effective coverage width, and standard lengths that manufacturers typically stock or produce routinely. Understanding these standard dimensions is crucial for several reasons:
- Cost Efficiency: Standard sizes are produced in high volumes, leading to significantly lower production costs and shorter lead times compared to fully bespoke sizes. Opting for common sizes leverages economies of scale, directly benefiting your project budget.
- Immediate Availability: Common sizes are often held in stock or have predictable production slots. This translates to faster project starts and reduced risk of construction delays waiting for materials.
- Design & Compatibility: Architects and engineers design structures based on known standard dimensions. Using common sizes ensures seamless compatibility with standard purlin spacings, clipping systems, and ancillary components (flashings, ridge caps, gutters), simplifying design, detailing, and installation. Deviations can require costly redesigns or custom fabrication of supporting elements.
- Predictable Performance: The structural performance (load tables) and weathertightness of IBR systems are rigorously tested and certified based on their standard profile dimensions and material specifications. Using common sizes guarantees you are utilizing a solution with proven, reliable performance data.
Demystifying IBR Sheet Common Sizes: A Technical Breakdown
Selecting the right IBR sheet involves specifying three core dimensional parameters:
Material Thickness (Gauge):
- Common Range: Typically 0.35mm (approx. 26 gauge) to 0.70mm (approx. 22 gauge) for standard applications. Thicker options (0.80mm, 1.00mm) are available for high-load or extreme condition applications.
- Measurement: Stated in millimeters (mm), often also referenced by gauge number (though gauge systems vary slightly).
- Impact: Thickness directly governs strength, rigidity, spanning capability, durability, and cost. Thicker gauges handle heavier loads (snow, wind uplift, foot traffic) and span wider purlin spacings but cost more per square meter.
- Common Choices: 0.40mm, 0.47mm, 0.50mm are extremely popular for roofs and walls in commercial/industrial buildings. 0.60mm offers enhanced durability for demanding environments.
Effective Coverage Width:
Definition: The width of roof or wall area that one IBR sheet actually covers when installed, accounting for the side-lap (where adjacent sheets overlap). This is the dimension that matters for calculating how many sheets you need per square meter.
Common Standard Widths: Two widths dominate global markets:
- 686mm Effective Coverage: This is arguably the most prevalent IBR size worldwide, particularly strong in Africa, the Middle East, and many parts of Asia. Offers a good balance of coverage and material efficiency.
- 762mm Effective Coverage: Also very common, especially in regions like Australia, New Zealand, and specific European markets. Provides slightly wider coverage per sheet.
Key Distinction: The overall width of the sheet as it comes off the coil is larger (typically ~1000mm or 1035mm) before profiling. The profiling process forms the ribs, reducing the flat coverage area. Always specify and order based on the Effective Coverage Width. Confusing overall width with coverage width leads to significant material shortages.
Length:
Standard vs. Custom: While manufacturers offer standard lengths (e.g., 2.0m, 3.0m, 6.0m) for stock purposes, the true power of IBR lies in custom cut-to-length production.
Custom Length Advantage: Producing sheets to the exact length required for your specific roof or wall bay minimizes:
- Waste: Zero cutting waste on-site.
- Labor: Eliminates time-consuming and potentially hazardous on-site cutting.
- Leak Points: Removes the need for unnecessary end-laps within a single bay, enhancing weathertightness.
- Aesthetics: Creates clean, continuous lines from ridge to eave.
Capability: Reputable manufacturers can typically produce lengths from 1.5 meters up to 12 meters or more on modern roll-forming lines, accommodating virtually any project requirement. Specify exact ridge-to-eave measurements.
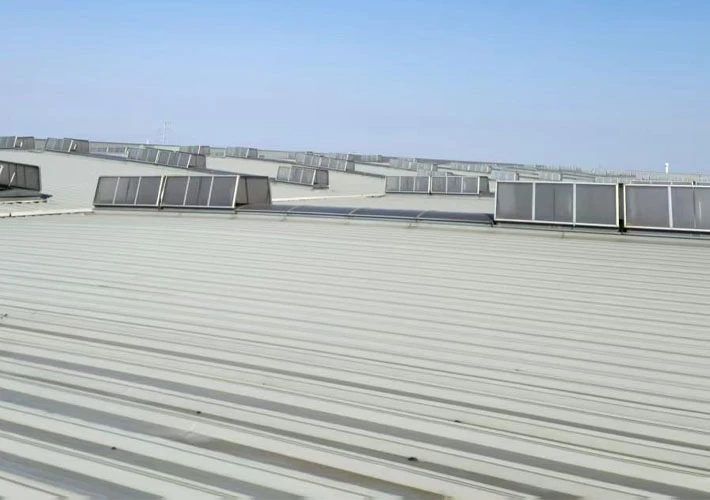
Beyond the Basics: Material Specifications & Coatings
The dimensions are critical, but the material itself defines longevity:
Base Steel: High-quality structural grade steel (e.g., G550 minimum yield strength) is essential for performance.
Corrosion Protection:
- Galvanized (GI): Zinc coating (e.g., Z275 – 275g/m² total) provides excellent basic protection. Common for internal walls or less corrosive environments.
- Galvalume®/Zincalume® (AZ): Aluminum-Zinc alloy coating (e.g., AZ150 – 150g/m² total) offers superior cut-edge corrosion resistance and heat reflectivity compared to standard GI. The preferred choice for most roofing applications globally.
Paint Systems (PPGI/PPGL): Pre-Painted Galvanized or Galvalume sheets offer aesthetic appeal and enhanced durability. Specify:
- Coating: Polyester (PE), Silicon Modified Polyester (SMP), Polyvinylidene Fluoride (PVDF).
- Thickness: Standard (e.g., 25μm) or High-Performance (e.g., 35μm).
- Color: Extensive RAL and custom color options. PVDF offers superior color and chalk resistance.
Optimizing IBR Sheet Selection: Matching Size to Project Needs
Choosing the optimal common size isn’t guesswork; it’s a calculated decision based on project specifics:
Structural Requirements:
- Load Analysis: Consult structural load tables provided by manufacturers or engineers. These tables show the maximum allowable purlin spacing for a given IBR thickness/gauge under specific dead loads (sheet weight, insulation), live loads (snow, maintenance), and wind loads (uplift, downforce).
- Spanning Needs: Wider purlin spacings demand thicker gauge sheets or stronger profiles. 0.47mm or 0.50mm IBR is often the minimum for typical industrial roof spans (1.5m purlins). 0.60mm+ is needed for longer spans or heavy snow loads.
- Wind Uplift: Critical for roofing. Thicker gauges and secure fastening systems (screws, clips) rated for the calculated uplift force are essential. The sheet profile itself contributes to resistance.
Functional Application:
- Roofing: Prioritize weathertightness, spanning capability, and wind uplift resistance. 686mm or 762mm coverage widths are standard. Thickness typically 0.47mm to 0.60mm. Galvalume® coating strongly recommended.
- Cladding/Walls: Can often use slightly thinner gauges (0.40mm to 0.50mm) as loads are generally lower than roofs. Aesthetics (color, finish) become more prominent. Effective coverage width choice depends on desired visual rhythm.
- Lining/Internal Use: Thinner gauges (0.35mm to 0.40mm) and galvanized coating are often sufficient.
Budget & Logistics:
- Cost Sensitivity: Thinner gauges and standard stock sizes offer the lowest initial cost. Balance this against long-term durability needs.
- Transportation: Consider trucking constraints. Custom lengths optimize packing and reduce site handling but need precise measurement. Very long sheets (>12m) require specialized transport.
- Installation Efficiency: Wider coverage widths (762mm) can slightly reduce the number of sheets and side-laps, speeding installation. Custom lengths eliminate on-site cutting time.
The Unmatched Advantage of Partnering with a Chinese Manufacturer
Sourcing your IBR sheets directly from a reputable Chinese factory like ours isn’t just about cost savings; it’s about accessing world-class manufacturing capability and strategic partnership:
1.Scale & Cost Leadership:
- Unrivaled Production Capacity: Benefit from vast, modern facilities capable of high-volume output without compromising quality or lead times.
- Direct Factory Pricing: Eliminate unnecessary markups from intermediaries. Our competitive pricing on common sizes is backed by efficient large-scale production and optimized supply chains.
- Material Sourcing Advantage: Direct access to top-tier Chinese steel mills (e.g., Baosteel, HBIS) ensures consistent supply of high-grade G550 AZ150/GI Z275 base materials at favorable rates.
2.Precision Manufacturing & Quality Control:
- State-of-the-Art Roll Forming: Our automated lines feature precision tooling and laser measurement systems, guaranteeing that every sheet meets exact dimensional tolerances (±0.5mm width, ±1mm length) and consistent profile geometry.
- Rigorous Multi-Stage QC: From coil inspection (coating weight, surface defects) to in-line profile monitoring and final dimensional checks, our quality protocols meet or exceed ISO 9001 standards and international building code requirements (AS/NZS 2728, SANS 357, BS EN 10169).
- Certifications: We hold relevant product certifications (e.g., for corrosion resistance, structural performance) and provide comprehensive Mill Test Certificates (MTCs) with every batch.
3.Flexibility & Customization Power:
- True Cut-to-Length Expertise: Go beyond standard stock lengths. Specify your exact ridge-to-eave measurement (within machine capabilities), and we produce sheets ready to install, eliminating waste and labor. Minimum order quantities (MOQs) are project-friendly.
- Comprehensive Coating & Color Options: Whether you require standard Galvanized (Z275), superior Galvalume® (AZ150), or a vast palette of pre-painted finishes (PE, SMP, PVDF in any RAL or custom color), we deliver precisely to specification. Access high-performance coatings (PVDF) at highly competitive rates.
- Responsive Engineering Support: Our technical team can advise on profile selection, load tables, fastener requirements, and detailing for complex projects.
4.Global Logistics Mastery:
- Export Experience: We are specialists in packing IBR sheets for maximum protection during long-distance ocean freight (using sturdy wooden crates/packs and edge protection).
- Efficient Shipping: Established relationships with major freight forwarders ensure reliable scheduling and cost-optimized routing to major ports worldwide (Rotterdam, Jebel Ali, Durban, Sydney, Los Angeles, etc.).
- Documentation: We handle all export documentation (Commercial Invoice, Packing List, Bill of Lading, Certificate of Origin) accurately and efficiently.
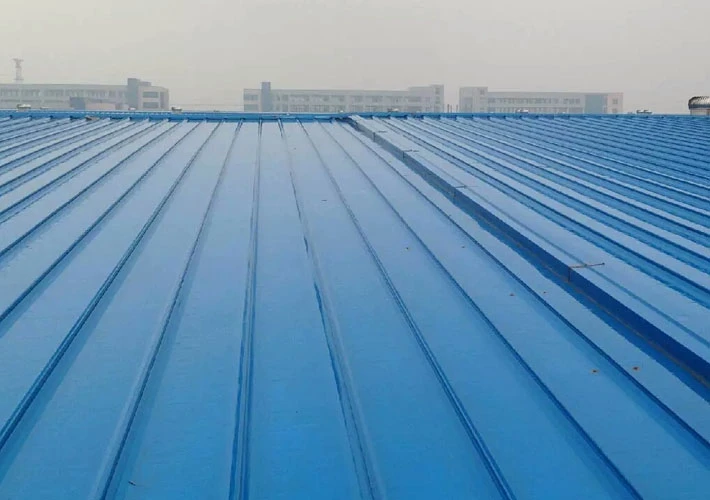
Why Settle for Generic? Partner with Precision IBR Sheet Experts
In the high-stakes world of commercial and industrial construction, the structural integrity, longevity, and cost-effectiveness of your building envelope hinge on the quality and suitability of your cladding materials. Off-the-shelf solutions or suppliers lacking deep manufacturing expertise introduce unnecessary risk.
Partnering with our specialized IBR sheet factory provides a distinct competitive edge:
- Guaranteed Specification Compliance: Receive sheets manufactured exactly to your required common size (thickness, effective coverage width, exact length), coating specification (Galvalume® AZ150, PPGI Color X), and performance standards.
- Uncompromised Quality: Benefit from rigorous Chinese manufacturing discipline and advanced quality control systems, ensuring every sheet performs as engineered.
- Significant Cost Savings: Leverage direct factory pricing and efficient production for the best value without sacrificing quality.
- Seamless Project Execution: Reliable supply of precisely dimensioned, custom-length sheets minimizes site waste, labor, and delays.
- Technical Partnership: Access knowledgeable support for optimal product selection and application detailing.
Ready to Specify with Confidence? Get Your Exact IBR Sheet Quote Today!
Stop searching through generic catalogs. Experience the precision, value, and partnership of sourcing your IBR sheet common size requirements directly from a leading Chinese manufacturer.