Overview and Composition of FRP Sheets
Fiber Reinforced Plastics (FRP) are a class of engineered composite materials consisting of a polymer matrix (such as epoxy, polyester, or vinyl ester resin) reinforced with fibers (like glass fiber, carbon fiber, aramid fiber, or basalt fiber).
- Resin matrix: Binds the fibers and determines the chemical resistance, thermal properties, and rigidity.
- Reinforcing fibers: Carry most of the load and provide high strength and stiffness.
- Interface bonding: The fiber-resin interface is critical for load transfer and crack resistance.
- Forming process: FRP sheets can be manufactured through methods such as hand lay-up, spray-up, pultrusion, hot press molding, or prepreg lamination.
By fiber type:
- GFRP (Glass Fiber Reinforced Plastic): Cost-effective with good strength, lightweight, non-conductive, and corrosion-resistant.
- CFRP (Carbon Fiber Reinforced Plastic): Extremely high strength-to-weight and stiffness-to-weight ratios; commonly used in aerospace and automotive.
- BFRP, AFRP, Basalt fibers, etc.: Offer specialized performance like heat resistance, impact resistance, and chemical durability.
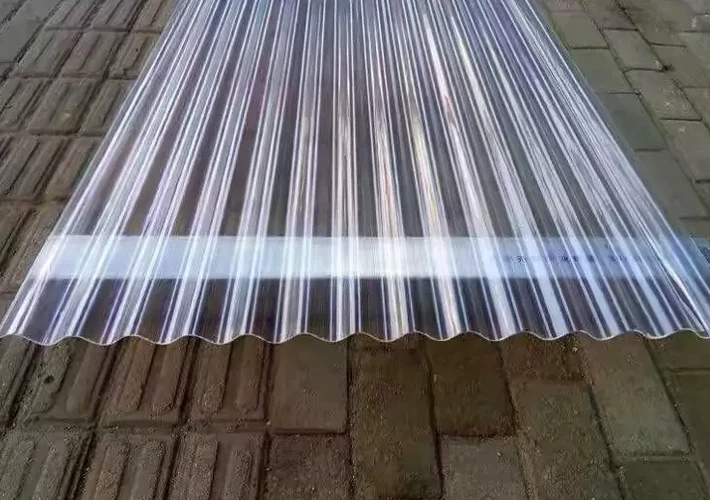
Performance Advantages of FRP Sheets
1.High Strength-to-Weight and Stiffness-to-Weight Ratios
- Lightweight: FRP weighs only 1/4 to 1/5 of steel, yet provides comparable or superior strength.
- Excellent mechanical performance: Especially CFRP, which allows significant structural weight reduction while maintaining high load-bearing capacity.
2.Corrosion and Chemical Resistance
- Outstanding durability in harsh environments: Excellent resistance to acids, alkalis, salts, and solvents.
- Ideal for corrosive environments: Widely used in chemical plants, wastewater facilities, and marine engineering.
3.Long Service Life and Low Maintenance
- FRP materials have high UV resistance and can withstand salt spray, thermal cycling, and humidity without degradation.
- Low maintenance: No rust, rot, or decay, significantly reducing long-term costs.
4.Flexible Design and One-Piece Molding
- FRP allows for complex shapes (curves, domes, honeycomb structures) through layup or pultrusion.
- Reduced mechanical joints: Large integrated parts can reduce part count by over 90% in aerospace applications.
5.Excellent Mechanical Properties
- High impact resistance: FRP grating can withstand high loads.
- Fatigue resistance: Better than many metals under cyclic loading.
- Outstanding seismic performance: Good for wind and shock resistance.
6.Electrical and Thermal Insulation
- Non-conductive: Suitable for electrical enclosures and telecom structures.
- Thermal insulation: Low thermal conductivity; useful for cold storage or insulation panels.
7.Fire Resistance and Flame Retardancy
- Flame-retardant FRP can be formulated with additives or special resins (e.g., fire-resistant vinyl ester).
- Complies with building fire codes in many public-use applications.
8.Insect and Biological Resistance
- Unlike wood, FRP is immune to mold, mildew, termites, and rot.
- Suitable for humid, tropical, or pest-heavy environments.
9.Fast Installation and Construction Time Savings
- Lightweight and modular: Easy to transport, assemble, and install.
- Reduced labor and time: Prefabricated panels simplify construction logistics.
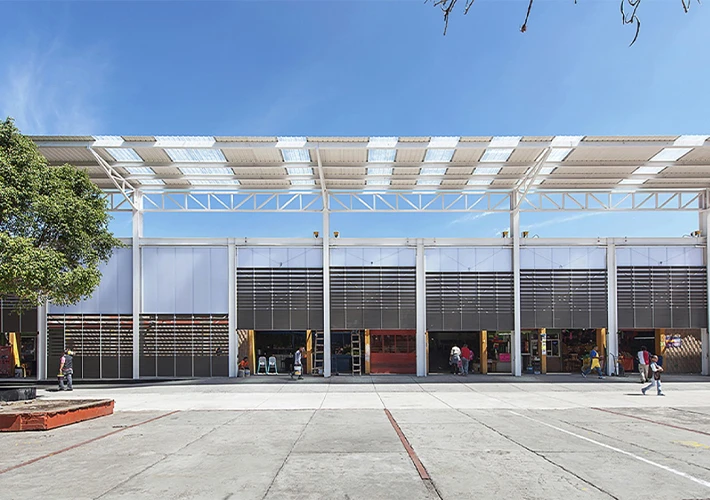
Common Applications of FRP Sheets
1.Construction and Infrastructure
- Building facades, wall panels, roofing, bridge deck panels, structural walkways, etc.
- Used in municipal infrastructure like cooling towers, cable trays, sewage systems.
- Increasingly adopted in modular and green building systems.
2.Transportation and Automotive
- Car body panels, underbody protection, interior structural parts.
- Aircraft cabin parts, wing components, or landing gear structures.
- Rail and electric vehicle components benefit from weight savings.
3.Marine and Offshore
- Hulls, decks, marine structures requiring corrosion and salt resistance.
- Ideal for docks, boats, oil platforms, and floating structures.
4.Renewable Energy
- Wind energy: Wind turbine blades are mostly CFRP or hybrid FRP.
- Solar energy: FRP used in support structures and panel frames.
5.Industrial and Chemical Facilities
- Chemical-resistant tanks, piping, ducts, and enclosures.
- Structural protection in harsh chemical environments.
6.Consumer Products and Specialty Structures
- Sporting goods, furniture, exhibition structures, artistic architecture.
- Hurricane shelters and bullet-resistant panels in disaster-prone areas.
Global Market Size and Demand Trends
A. Market Size & Forecasts
- 2024: ~$1.709 billion USD
- 2032: Projected to reach ~$2.926 billion USD (CAGR ~6.47%)
- Other reports estimate even higher figures up to $5.14 billion by 2033.
- Consistently strong growth rate across regions and applications.
B. Regional Analysis
- Asia-Pacific: Largest and fastest-growing market (~40% market share), led by China, India, and Japan.
- North America: ~30% share, driven by construction, automotive, and regulatory policies.
- Europe: ~20%, emphasizing sustainability and performance.
- LATAM, Middle East, Africa: Emerging markets with increasing infrastructure needs.
C. By Fiber Type & Product Segment
- GFRP: Dominates with 50–60% share due to balanced cost and performance.
- CFRP: Fastest-growing, ~30% share, high-end applications.
- Special fibers: AFRP, BFRP ~10–20%, niche but expanding.
- Solid panels: ~60% market share; honeycomb, sandwich, and laminate panels also rising.
D. Growth Drivers
Lightweight & Energy-Efficient Systems
Demand from aerospace, automotive, EVs for weight reduction and performance.
Urbanization & Infrastructure Upgrades
Public transportation, bridges, water treatment driving durable materials adoption.
Environmental Policies
Sustainable construction and low-VOC building materials boost FRP adoption.
Technology Advancements
Automation, resin innovation, embedded smart sensors, fireproof coatings.
Emerging Application Fields
Aerospace, wind energy, prefab buildings, intelligent power enclosures, etc.
E. Constraints and Challenges
High Initial Cost
FRP costs more than traditional materials; pricing sensitivity in some regions.
Recycling Challenges
Thermoset-based FRP is difficult to recycle; mechanical and chemical recovery methods are still developing.
Lack of Standardization
Product inconsistency among manufacturers; standard testing and certifications needed.
Material Competition
Metals and concrete still dominate due to cost and supply chain maturity.
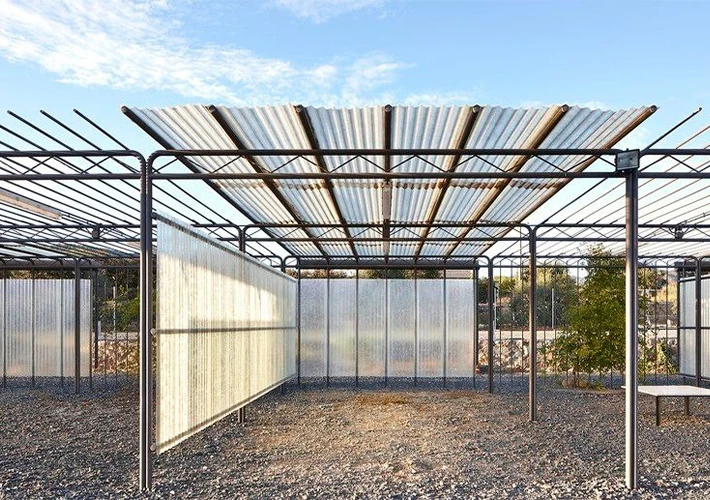
Real-World Feedback and Case Studies
- DIY campers and trailers: Users report no cracking or brittleness in FRP panels after years of UV exposure.
- Commercial kitchens/bathrooms: Properly sealed FRP panels remain mold-free and durable in humid conditions.
- Hurricane shelters in Florida: Some designs use FRP structures rated for 250 MPH wind loads and projectile resistance, though costs remain high.
Summary and Future Outlook
Key Performance Advantages
- Lightweight, high strength
- Excellent corrosion and weather resistance
- Long service life, minimal maintenance
- Versatile design and complex shaping
- Electrical and thermal insulation
- Flame retardancy and biological resistance
- Easy installation, time-saving construction
Global Demand Trends
- Steady global growth (6–7% CAGR) in all major reports
- Applications expanding in construction, transport, energy, and infrastructure
- Asia-Pacific leading growth; North America and Europe with strong demand
- Technological advancements fueling product quality and variety
Future Opportunities
- Improve recyclability with thermoplastics or biodegradable resins
- Standardize quality through testing protocols and certifications
- Hybrid fiber systems: Combine performance and cost-effectiveness
- Smart structures: Integrate sensors for health monitoring
- Green resin systems: Bio-based, fire-resistant, or low-emission resins
Conclusion
In summary, FRP sheets are rapidly becoming essential materials in modern engineering, thanks to their superior strength-to-weight ratios, corrosion resistance, long service life, and flexible design potential. As industries continue to demand more efficient, sustainable, and high-performance materials, FRP’s role in global construction, transportation, renewable energy, and industrial sectors will only grow stronger.
Though challenges like recyclability and cost remain, ongoing R&D and regulatory support will likely push the FRP industry toward more standardized, sustainable, and innovative solutions in the coming decade.