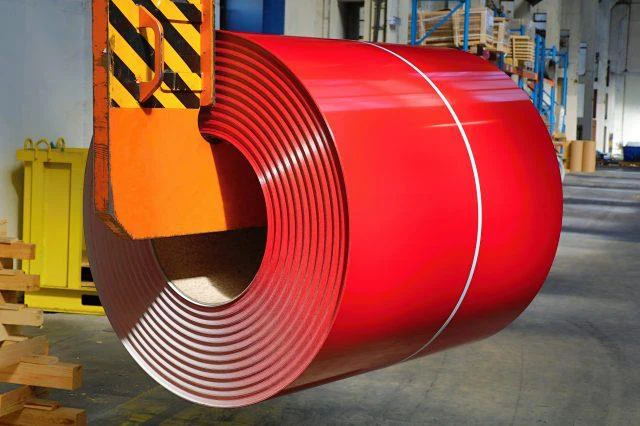
PPGl (Pre-Painted Galvalume) and PPGL (Pre-Painted Galvanized Iron) are both types of coated steel used in various industries. The choice between the two depends on specific requirements such as the application, environmental conditions, and budget.
let’s delve deeper into the differences between PPGl and PPGL:
1. Composition:
- PPGl (Pre-Painted Galvalume):
- Galvalume is a trademarked name for a type of steel product that consists of a coating of aluminum-zinc alloy on the base steel.
- The aluminum in the coating provides sacrificial protection to the underlying steel, enhancing corrosion resistance.
- The combination of zinc and aluminum offers superior corrosion resistance compared to traditional galvanized steel, particularly in harsh environments.
- PPGL (Pre-Painted Galvanized Iron):
- PPGL is typically made from galvanized steel, which is steel that has been coated with a layer of zinc through a hot-dip process.
- The zinc coating acts as a barrier between the steel substrate and the surrounding environment, protecting the steel from corrosion.
- While zinc provides good corrosion resistance, it may not offer the same level of protection as the aluminum-zinc alloy in Galvalume, especially in more corrosive environments.
2. Corrosion Resistance:
- PPGl:
- Offers excellent corrosion resistance, particularly in harsh environments such as coastal areas, industrial zones, or regions with high levels of atmospheric pollutants.
- The combination of zinc and aluminum provides enhanced protection against corrosion, even in aggressive environments.
- PPGL:
- Provides good corrosion resistance, suitable for many applications where moderate protection against rust is required.
- May not be as effective as PPGl in highly corrosive environments, but still offers adequate protection in most cases.
3. Cost:
- PPGl:
- Generally more expensive than PPGL due to the added benefits of the aluminum-zinc alloy coating.
- The superior corrosion resistance and longevity of PPGl may justify the higher initial cost, especially in applications where corrosion is a significant concern.
- PPGL:
- Typically more cost-effective than PPGl, making it a preferred choice for applications where budget constraints are a primary consideration.
- While it may not offer the same level of corrosion resistance as PPGl, PPGL still provides adequate protection for many applications at a lower cost.
4. Applications:
- PPGl:
- Ideal for applications where corrosion resistance is critical, such as roofing, siding, automotive parts, and outdoor structures.
- Well-suited for use in environments with high humidity, salt spray, or industrial pollutants.
- PPGL:
- Widely used in various industries, including construction, automotive, appliances, and HVAC.
- Suitable for applications where moderate corrosion resistance is sufficient, such as indoor construction, household appliances, and general fabrication.
In summary, PPGl and PPGL offer different levels of corrosion resistance and cost-effectiveness, making them suitable for different applications and environments. PPGl provides superior corrosion protection but comes at a higher cost, while PPGL offers good corrosion resistance at a lower price point. The choice between the two depends on specific project requirements, budget constraints, and environmental factors.