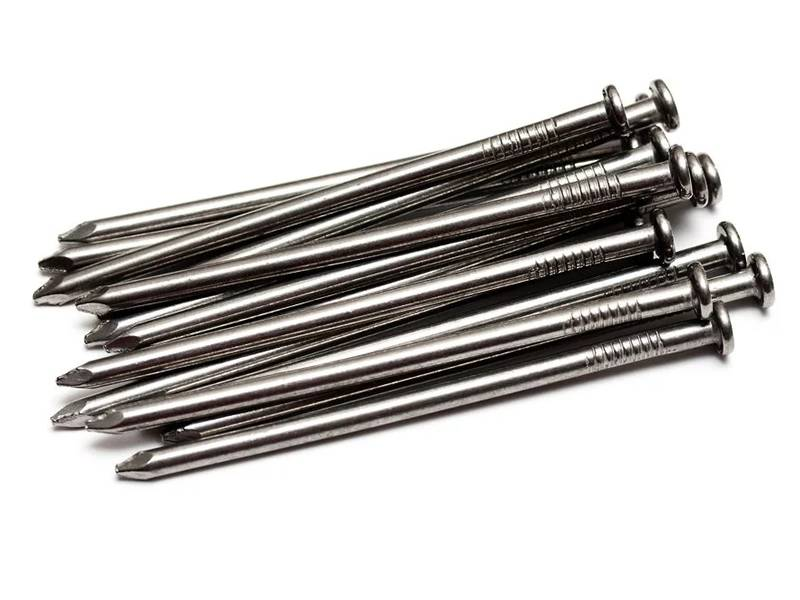
The making process of common nails usually includes the following steps:
1.Raw material preparation
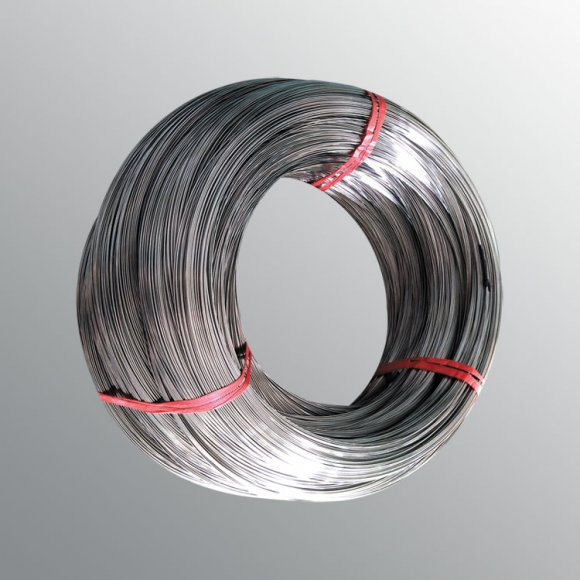
The main raw material of screws is metal wire. Commonly used materials include carbon steel, stainless steel, copper, etc. These metal wires need to undergo quality inspection to ensure that they meet manufacturing requirements.
2.Wire drawing
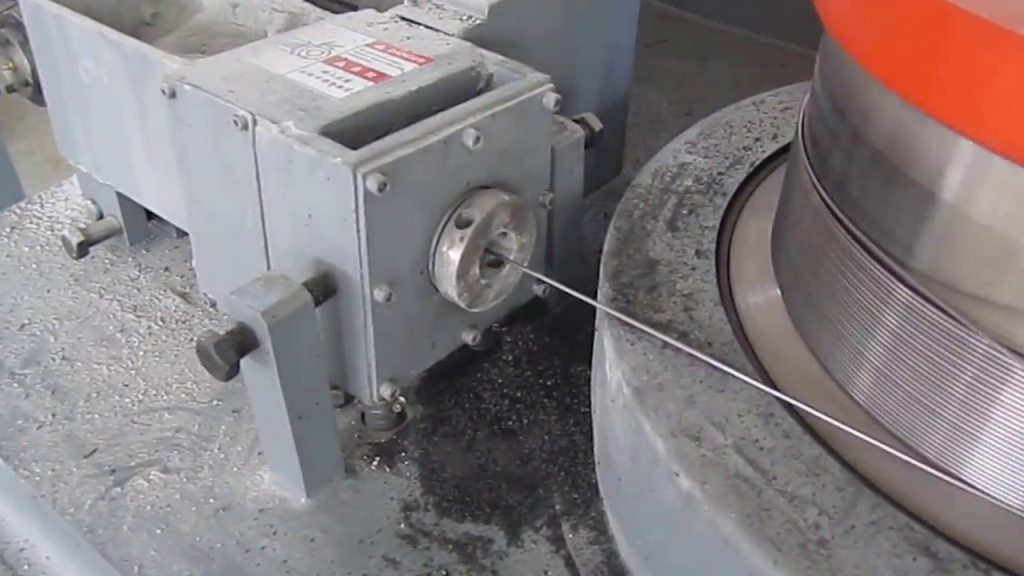
- Raw Material Preparation: The main raw material for screws is metal wire, commonly made from materials such as carbon steel, stainless steel, or copper. These metal wires undergo quality inspection to ensure they meet manufacturing requirements.
- Wire Drawing: Selecting appropriately sized metal wire, the wire is processed into the initial shape of the screw through a drawing process. This step typically involves cold or hot working methods to gradually reduce the diameter of the metal wire and form the basic external shape of the screw.
- Header Cold Forging: One end of the wire is processed into the head of the screw using a cold forging machine. This process includes pressing the wire into the appropriate shape, forming threads, and creating the screw head.
- Overall Cutting: The formed metal wire is cut according to the length specifications of the screw, creating individual screws.
- Heat Treatment: To enhance the hardness and strength of the screw, heat treatment is usually performed. This involves heating the screw to a specific temperature and then rapidly cooling it to alter the metal’s crystal structure.
- Surface Treatment: Surface treatments such as galvanization, nickel plating, or other corrosion-resistant processes may be applied to improve the screw’s corrosion resistance.
- Quality Inspection: The screws undergo quality checks to ensure they meet relevant standards and specifications.
- Packaging: Screws that meet quality standards are packaged, typically in boxes or bags, for transportation and sale.
3.Header Cold Heading
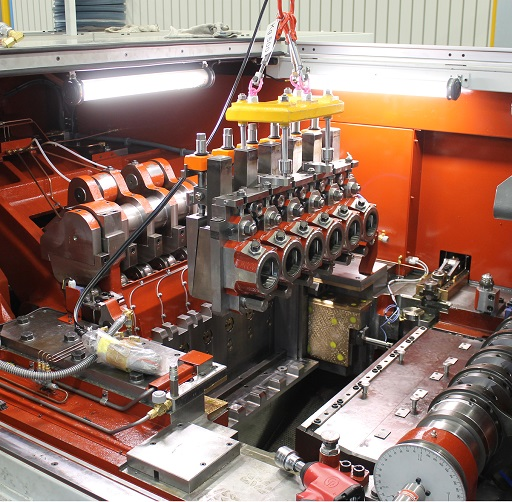
- Wire Preparation: After the wire drawing process, the metal wire is prepared for the cold heading operation.
- Cold Heading: The prepared metal wire is subjected to the cold heading process. In this step, one end of the wire is shaped into the head of the screw using a cold heading machine. The cold heading machine applies pressure to the metal, deforming it to create the desired shape, including forming threads and shaping the screw head.
- Forming Threads: As part of the cold heading process, threads are formed on the screw. This involves precision shaping and molding of the metal to create the threaded portion of the screw.
- Screw Head Formation: The cold heading machine shapes the end of the wire into the specific configuration required for the screw head, ensuring uniformity and precision in the manufacturing process.
- Quality Control: The products from the cold heading process are subjected to quality control measures to ensure that they meet the specified standards and requirements.
4.Overall Cutting
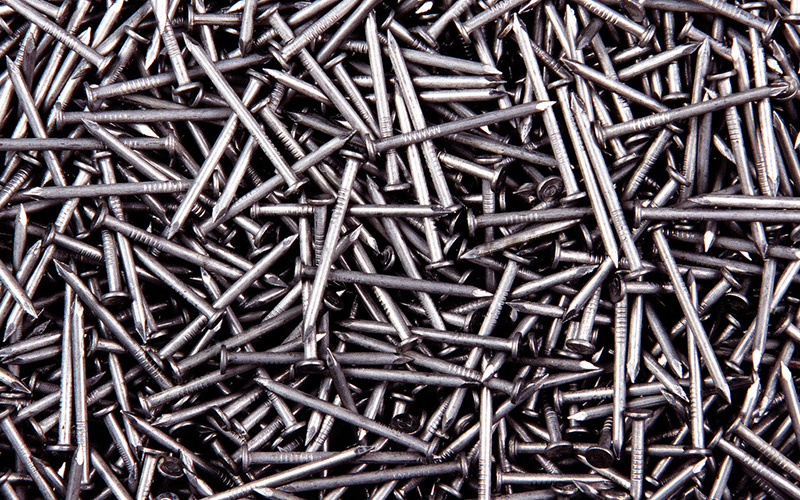
- Cutting to Length: After the cold heading process, the formed metal wire is cut to the desired length to create individual screws.
- Precision Cutting: Utilizing cutting equipment, the metal wire is precisely cut at specified intervals, ensuring uniformity in the length of the screws.
- End Finishing: Following the cutting process, any necessary finishing touches are applied to the cut ends of the screws to achieve the desired shape and dimensions.
- Quality Inspection: The screws undergo a quality inspection to verify that they meet the required standards and specifications.
- Packaging: After passing quality control, the screws are packaged for transportation and sale, often in boxes or bags.
5.Heat Treatment
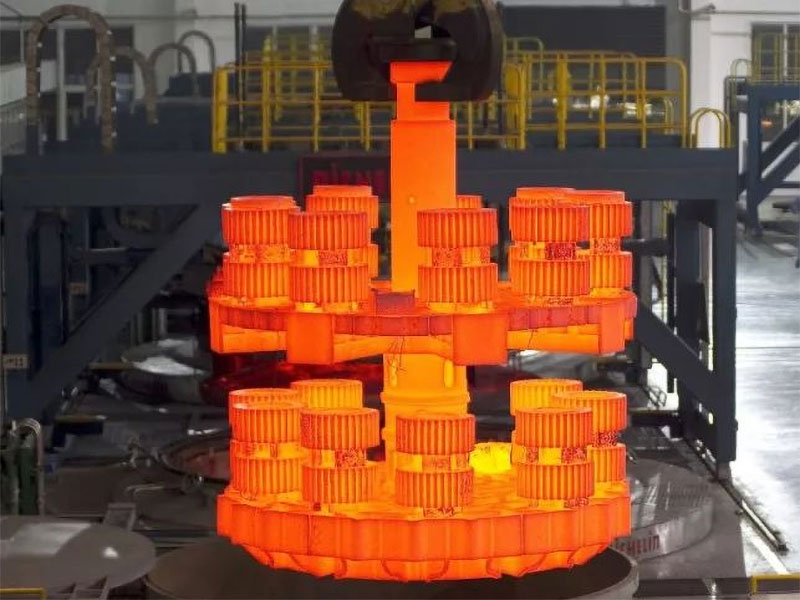
- Heating: The screws are subjected to controlled heating to achieve a specific temperature, typically in a furnace or similar equipment.
- Soaking: The heated screws are allowed to soak or dwell at the specified temperature for a predetermined period. This step ensures uniform heating throughout the material.
- Quenching: After soaking, the screws are rapidly cooled, or quenched, using methods such as water, oil, or air quenching. This rapid cooling alters the metal’s crystal structure, enhancing its hardness and strength.
- Tempering: In some cases, a tempering process follows quenching to reduce the brittleness introduced during the rapid cooling. Tempering involves reheating the metal to a lower temperature and then allowing it to cool slowly.
- Inspection: The heat-treated screws undergo thorough inspection to ensure that they meet the required hardness and mechanical properties.
- Surface Inspection: The treated screws may also undergo surface inspection to check for any changes or irregularities in the appearance of the metal.
- Final Quality Check: A final quality check is performed to confirm that the screws meet the specified standards and performance criteria.
- Packaging: Following successful completion of the heat treatment and quality checks, the screws are packaged for distribution and use.
6.Surface Treatment
- Cleaning: The screws undergo a cleaning process to remove any contaminants or residues from the surface.
- Surface Preparation: The cleaned screws are prepared for surface treatment, which may involve pre-treatments such as etching or coating to enhance adhesion.
- Coating Application: A protective coating, such as zinc plating, nickel plating, or another corrosion-resistant material, is applied to the surface of the screws. This coating helps improve corrosion resistance and durability.
- Curing or Drying: After the coating is applied, the screws may go through a curing or drying process to ensure the coating adheres properly and forms a protective layer.
- Quality Inspection: The screws undergo a thorough inspection to check the quality and uniformity of the applied coating.
- Additional Treatments: Depending on the specific requirements, additional surface treatments may be applied, such as lubricants or sealants.
- Final Inspection: A final inspection is conducted to ensure that the screws meet the specified standards for surface finish and corrosion resistance.
- Packaging: Once the surface treatment is completed and the screws pass quality checks, they are packaged for distribution and use.
7.Quality inspection
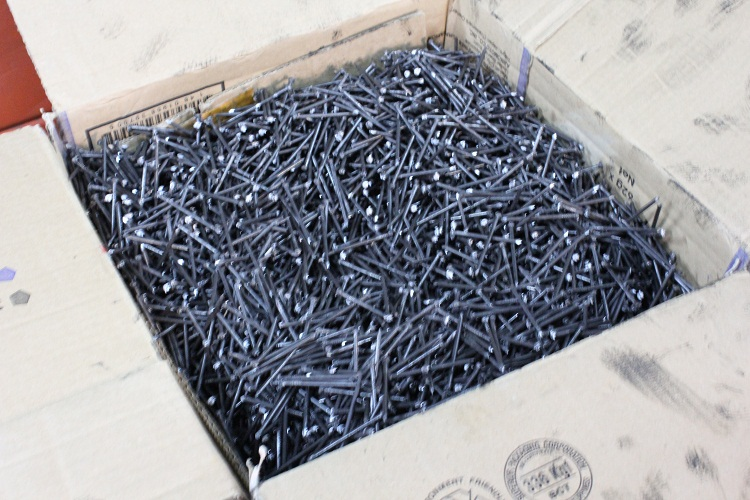
Quality inspection of screws to ensure they comply with relevant standards and regulations.
8.Packaging
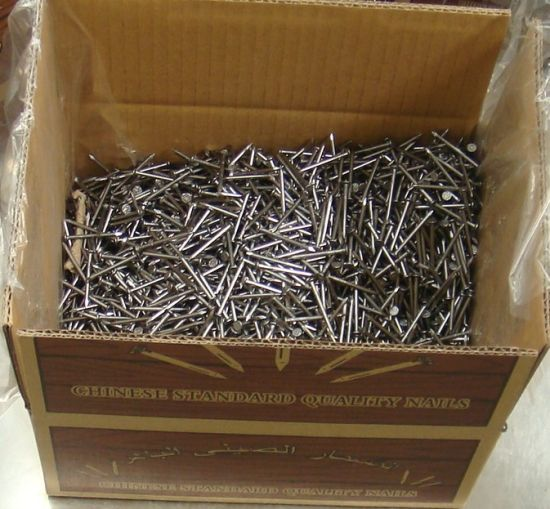
Screws that meet quality standards are packaged, usually in boxes or bags, for easy transportation and sales.
There may be some variations in these steps depending on the type of screw, its purpose and manufacturing process. Screw manufacturing involves multiple processes, each of which requires precise control to ensure the quality and performance of the final product.